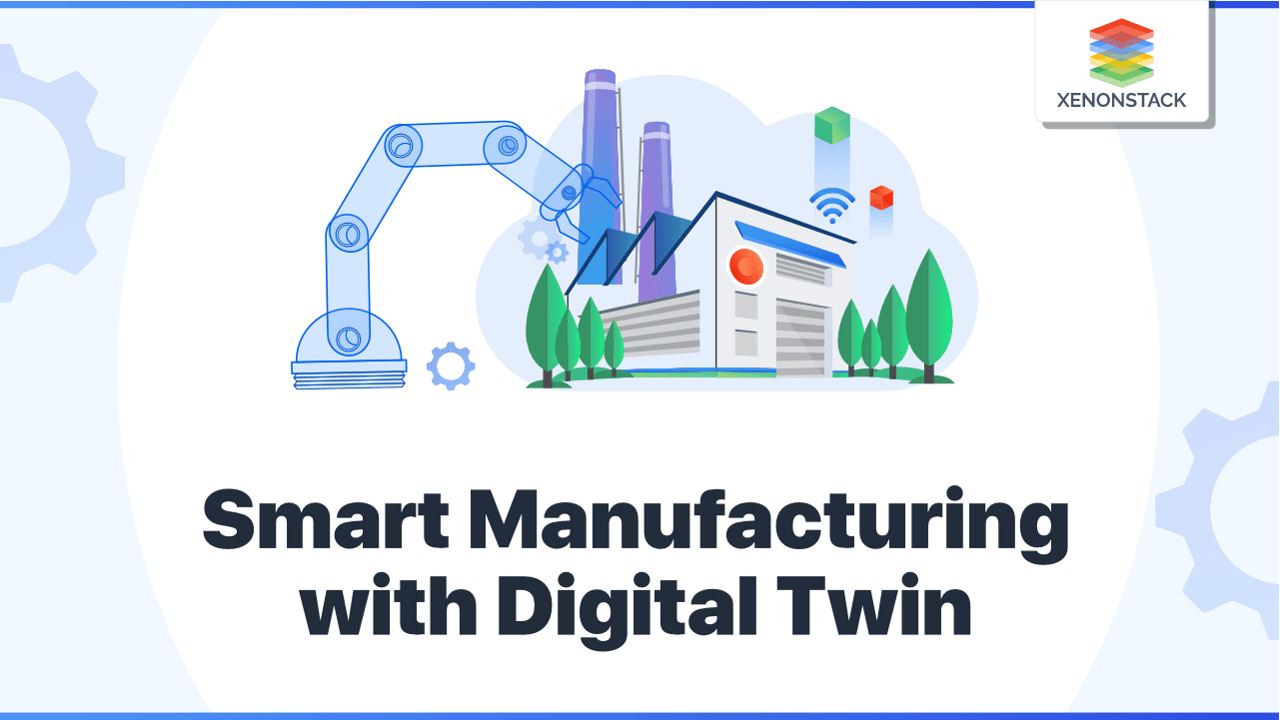
With the application of the advanced generation of IT, a new industrial revolution is in complete fluctuation. As a key component of Industry 4.0, many countries have launched manufacturing development strategies to drive innovation and efficiency. Among these new strategies, digital twin technology and innovative manufacturing have become essential for industrial development and the industrial revolution. Industry 4.0 digital twin solutions are highly valued by countries worldwide for enhancing productivity and streamlining operations.
Digital Twin Technology is more than a virtual model—it’s a dynamic, evolving replica that predicts, optimizes, and transforms real-world operations.
What is Smart Manufacturing, and What Is Its Role in Industry 4.0?
Smart Manufacturing (SM) is a technology-driven approach to monitoring production processes using machines connected to the Internet. Using data analysis, SM aims to automate operations and identify opportunities to improve manufacturing performance.
-
SM is a specific application of the Industrial Internet of Things (IIoT). Deployment involves embedding sensors in manufacturing machines to collect operational status and performance data. Previously, this information was stored in a local database for individual devices and was only used to identify the root cause after a device failure.
-
By analyzing data flowing from machines in the entire factory or multiple factories, manufacturing engineers and data analysts can look for signs that certain parts may be out of order or unplanned by predictive maintenance. One can avoid equipment downtime. Industry 4.0 digital twin technology enhances this process by providing real-time insights and simulations to optimize operations.
-
For example, the SM system can automatically order more raw materials than are in stock, assign other equipment to manufacturing orders as needed to complete the order, and prepare the distribution network once the order is completed. With Industry 4.0 digital twin solutions, manufacturers can enhance decision-making and streamline supply chain management.
Fig 1: Key Components of Digital Twin in Manufacturing
How Digital Twin Technology Works in Smart Manufacturing
Digital twin technology begins with applied data science, which researches a system or physical object's physics or mathematics and operational data to create a mathematical model that will simulate the original.
Key Steps in Digital Twin Technology
Data Collection & Modeling
Developers create virtual computer models that receive feedback from sensors collecting data from their real-world counterparts.
Real-Time Simulation & Insights
The digital twin mimics and simulates the actual version in real time, providing insights into performance, efficiency, and potential issues.
Scalability & Complexity
-
Digital twins can be as simple or complex as needed, depending on the data available.
-
The more data collected, the more accurate and responsive the simulation.
Prototyping & Testing
-
Digital twins can work alongside physical prototypes to validate designs before production.
-
They can also act as standalone prototypes, simulating real-world conditions to predict how the physical version will perform during manufacturing.
By leveraging Industry 4.0 digital twin technology, manufacturers can optimize production, enhance predictive maintenance, and improve overall operational efficiency.
Make smarter business choices with the right tools! Read here about the Top 5 Decision Analysis Tools for Businesses.
Top Challenges in Implementing Digital Twin Technology
The digital twin can be used in various industries, from power generation and automotive to the alternative. It has been used to solve various problems. These challenges include exhaust testing and corrosion resistance of offshore wind turbines and improving the efficiency of racing cars. Other applications include hospital modelling to determine workflows and staffing to find process improvements.
Digital twins allow users to explore product process improvement, product lifecycle extension, product development, and prototype testing solutions. In these cases, the digital twin can effectively represent a problem so that the solution can be developed and tested programmatically rather than in the real world.
Key Applications of Digital Twin in Industry 4.0
Digital twins are being used in various industries for many purposes and applications. Some of the examples are listed here:
-
Smart cities: Digital twins are getting used to helping cities become more environmentally, socially, and economically sustainable. Virtual models can guide planning decisions and solve many typical challenges modern cities face.
-
Healthcare: The medical department benefits from digital twins in areas such as surgery training, organ donation, and risk reduction during surgery. The system also models the flow of people through the hospital and tracks where the infection is and who may be at risk of contact.
-
Retail - Outside of industry and manufacturing, digital twins are used in retail to model and enhance the customer experience.
-
Disaster Management - Global climate change has affected the world in recent years, so digital twins can help counter this problem by creating more intelligent infrastructure, climate change monitoring, and emergency response plans.
AI adoption comes with hurdles—but the right solutions can drive success. Read here about Challenges and Solutions in AI Adoption.
Operational Benefits of Using Digital Twin in Manufacturing
-
Real-time Remote Monitoring: To get a detailed overview of an extensive physical system in real-time is often very difficult or even impossible. However, the digital twins can be accessed from anywhere, allowing users to monitor and control the system performance remotely.
-
Accelerated Risk Assessment and Production Time: Digital twins allow companies to validate and test products before they exist in the real world. By replicating the planned production process, engineers can identify errors before manufacturing begins, reducing costly design flaws and optimizing Industry 4.0 digital twin-driven production cycles.
-
Enhancing System Reliability Through Disruption: Engineers can disrupt the system to examine the system's reaction, synthesize unexpected scenarios, and identify corresponding mitigation strategies. This feature improves risk assessment, accelerates new product development, and increases production line reliability.
-
Better Team Collaboration: With 24/7 access to system data and automated processes, technicians can focus more on collaboration between teams, improving workflow efficiency and overall operational effectiveness. Industry 4.0 digital twin solutions enable seamless coordination between departments.
-
Predictive Maintenance: The IoT sensors in a digital twin system generate large amounts of data in real time, allowing enterprises to analyze the data to identify problems in the system proactively. This feature allows enterprises to plan predictive maintenance more accurately, improve production line efficiency, and reduce maintenance costs.
The Future of Digital Twin in Smart Manufacturing
Digital twins help companies create value, generate new revenue streams, and address key strategic questions. With advancements in Industry 4.0 digital twin technology, organizations can develop highly agile, cost-effective, and flexible digital twins with reduced capital investment and time constraints.
The future of digital twins is vast as increasing cognitive power and AI integration continue to enhance their capabilities. As a result, digital twins are constantly evolving, learning new skills, and refining their predictive insights. This allows businesses to optimize processes, improve efficiency, and drive innovation, ultimately leading to better products and more intelligent manufacturing in the future.
Next Steps in Adopting Digital Twin Technology
Talk to our experts about implementing digital twin technology and smart manufacturing solutions. Learn how industries and different departments leverage AI-driven workflows and predictive decision intelligence to enhance operational efficiency. Utilize industrial AI to automate and optimize manufacturing processes, improving productivity and agility.