
Nowadays, everyone wants to win customers. The competition is extreme, and everything has to be fast and efficient. Among all these things, to win and retain customers, we must ensure the good quality of the service provided and the products we manufacture. There needs to be more than the old quality control and inspection system for emerging technologies. This is why companies have started using quality engineering tools in which solutions are created in a way that meets the required standards. It's something new and necessary in today's emerging technology landscape.
A process to check the system accepts the requirements of a user or not. Click to explore about our, User Acceptance Testing Tools
What is Quality Engineering? Why is it Important in Modern Development?
Quality engineering is a process that applies stringent quality control measures at every stage of product development. It analyzes, develops, manages, and maintains quality assurance (QA) protocols. Quality assurance usually continues after a product has been delivered.
The goal of QE is to ensure the quality of the product right from the start, minimizing the potential loss caused by errors. Quality engineering differs from traditional quality control measures in that it is present throughout the production process. In traditional systems, quality is checked only at the final production stage. Meanwhile, traditional methods could be more efficient and lead to extra costs and labor.
Top Quality Engineering Tools and Methodologies for Improved Efficiency
Quality engineering tools and methods are developed using a horizontal approach. It involves many branches of business and engineering. Quality engineering tools include various methodologies such as:
-
Implement a Quality Management System (QMS).
-
Advanced Product Quality Planning (APQP) tools from design concept and verification to finish product tracking. Tools like Error Mode and Effects Analysis (FMEA) and Quality Function Deployment (QFD) are beneficial here.
-
Implement the voice of the customer (VOC) into new product designs and processes.
-
Identify and eliminate waste in business and production processes.
-
Coordinate with internal and external suppliers to ensure materials, assemblies, and components meet design and quality requirements.
-
Implement process controls such as Statistical Process Control (SPC).
-
Addressing the root cause: Implement practical root cause analysis (RCA) measures to separate signal from noise to identify the root cause of problems. This could be in the form of enhanced, AI-driven statistical process control from machine monitoring data or increased attention to human quality aspects gathered from device-driven applications.
-
Fix Root Cause: Ensure effective process control by developing appropriate test and inspection methods.
An approach which consolidates test first driven methodology and refactoring. Click to explore about our, Golang Unit Testing
Proven Strategies for Implementing Quality Engineering in Software Testing
Quality engineering tools provide solutions to design, implement, and maintain policies and procedures to ensure the quality of continuous testing in continuous delivery processes. This requires a deep understanding of assessment practices and technologies, including artificial intelligence (AI), big data analytics, and automation. Quality-engineered solutions help detect and prevent problems in software applications.
-
Process control and monitoring
-
Implement standards and metrics
-
Data collection and analysis
-
Test development
-
Identify problems and solutions
-
Follow up to ensure corrective action
Quality Engineering Best Practices for Continuous Improvement
-
Unit testing: Unit testing is the process of testing that measures the functional credibility of a specific software unit on a code level. Developers write test cases, run them and send them to the testing team.
-
Integration Testing: After the individual software units are tested, the focus shifts to testing the integrated units. Integration testing is used to test integrated units for their functionality. This testing can be conducted either by the tester, developer, or both.
-
System Testing: System testing measures the functionality of an integrated system.
-
Acceptance Testing: Acceptance testing measures the software's credibility based on the business objectives and criteria.
-
Performance Testing: Performance testing monitors the software’s stability and performance under specific scenarios.
-
Security Testing: Security is a crucial part of having quality software. This testing is conducted to measure security loopholes and save the software from security issues.
-
Usability and Compatibility Testing: This testing is done to measure the end-user’s interaction with the software and device compatibility issues.
Key factors for delivering quality engineering solutions beyond Software Testing:
-
Processes: Its consultants establish structured and collaborative processes. Bring standardization to create a quality environment that focuses not only on change but also on empowerment.
-
Metrics: Proper quality engineering metrics enable effective quality management. With the most advanced consistent methods, make customer satisfaction.
Big Data is the trend that is revolutionizing society and its organizations due to the capabilities it provides to take advantage of a wide variety of data. Click to explore about our, Big Data Testing Best Practices
Expert-Backed Quality Engineering Services to Drive Business Success
The various services of quality engineering tools include:
Quality Strategy
Defines a strategic approach to product quality that impacts every project, leveraging left-shifting principles, automation, and continuous testing.
Automated Testing
Applies automation to speed up testing, provide quick developer feedback, and enable continuous integration.
Process Standardization
Define and implement a common set of quality standards across your organization - balance flexibility and discipline with our built-in toolkit for engineering organizations.
Transformative Benefits of Quality Engineering in Industry 4.0 and Digital Transformation
-
Enhanced Feedback Loops – Organizations gain better visibility into processes with improved data analytics. Quality engineers can identify corrective and preventive actions more accurately and proactively. By analyzing data relationships, they can implement mechanisms to ensure quality at every stage of production.
-
Proactive Maintenance and Issue Prevention – Data from IoT-connected machines helps quality engineers predict potential issues, ensuring non-compliance is avoided. Operators can repair and maintain equipment before disruptions occur. Techniques like accelerated stress testing, real-time process monitoring, and AI-driven modeling enhance proactive quality engineering.
-
Integrated Quality Control Systems – Industry 4.0 enables quality engineers to embed quality control measures directly into machines and production processes. Advanced Quality Management Systems (QMSs) leverage artificial intelligence to refine system design, ensuring greater efficiency and precision with each iteration.
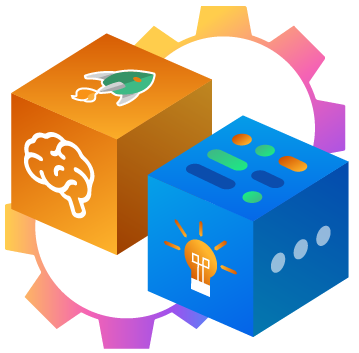
Why Quality Engineering Matters for Business Success
Quality engineering tools have immense benefits. QE enhances process efficiency, ensures product quality, and boosts customer satisfaction. It will have a positive impact on customer satisfaction. The customer’s voice can be heard using it methods and tools. They are used during product design, development, and implementation. Integrate this into product design so that quality is designed and built into the product. Waste is identified and eliminated during production. Its techniques can be done properly using the right tools. This can significantly increase the quality of the product.
Next Steps in Implementing Quality Engineering for Future-Ready Operations
Talk to our experts about implementing quality engineering, how industries and different departments leverage AI-powered testing workflows and intelligent automation to enhance software reliability. Utilize AI to automate and optimize quality assurance (QA) processes, ensuring higher efficiency, accuracy, and faster issue resolution.